Sewing the centuries together
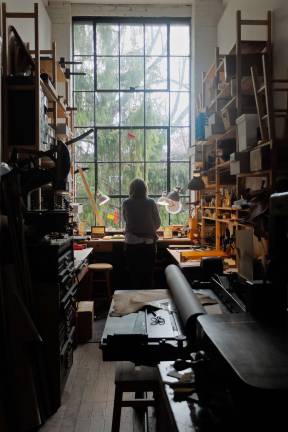
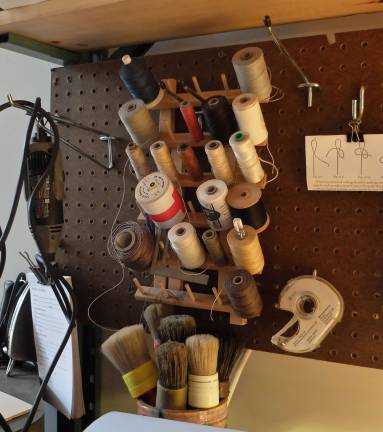
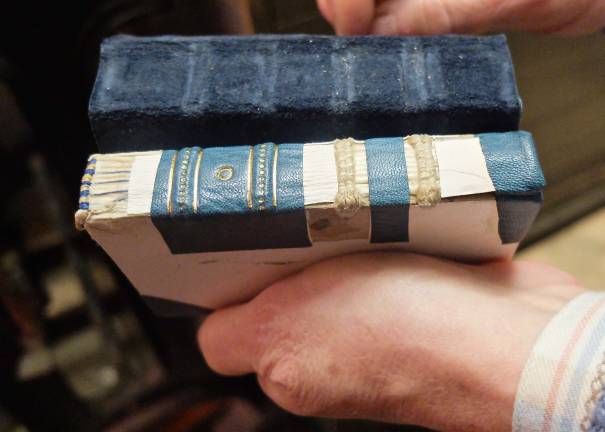
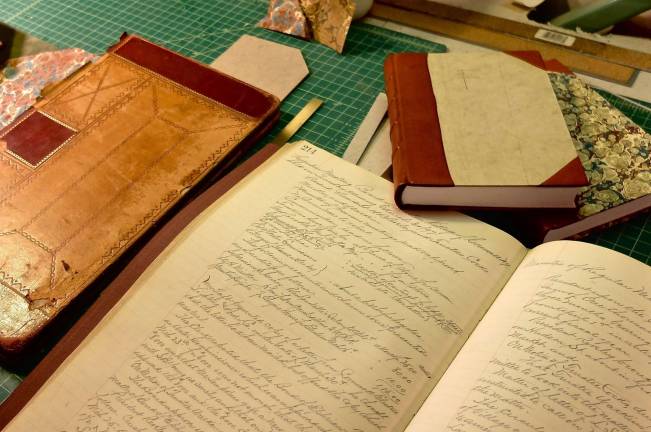
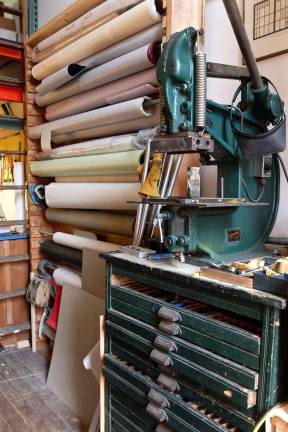
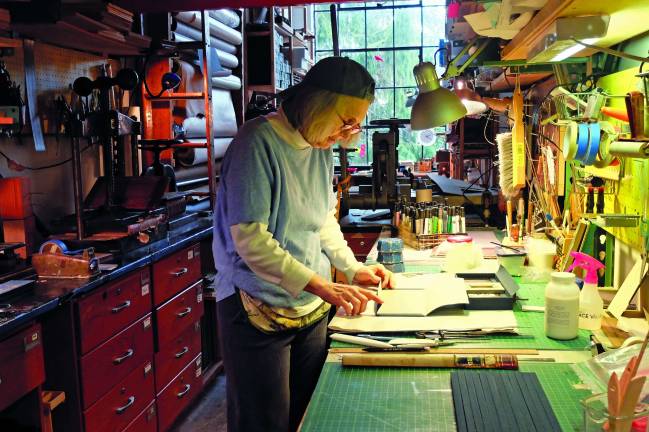
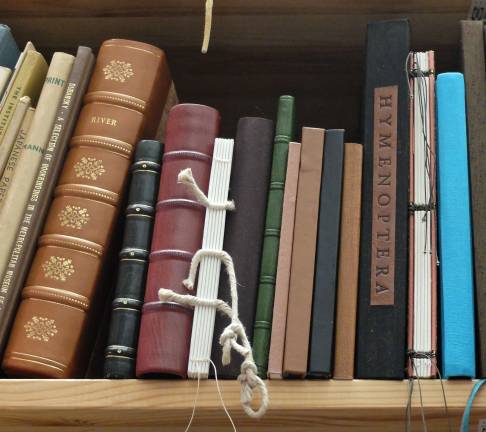
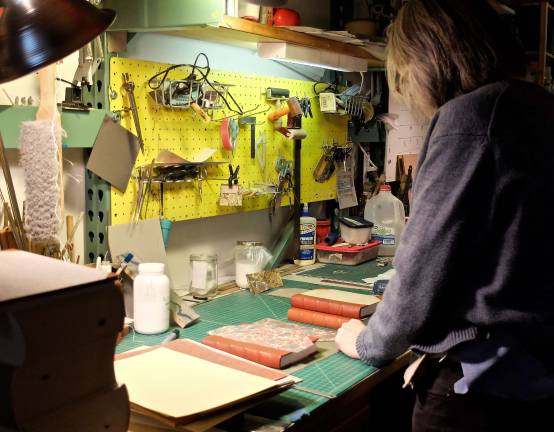
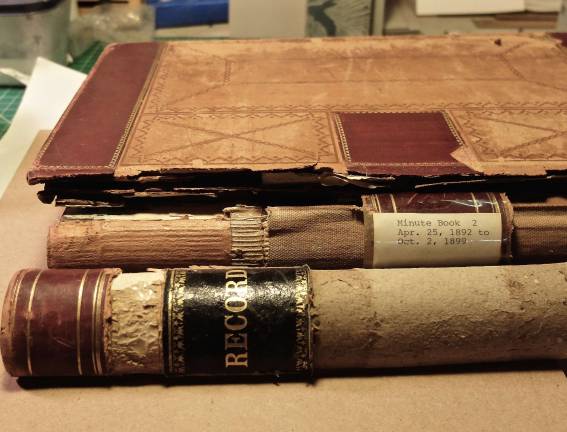
Behind the debris of a waterfront long past its prime is a repurposed factory. In a second floor studio shaped like the narrow hull of a ship, Alice Vaughan runs Hudson River Bindery, her one-woman show. Several large vintage cutting and pressing machines line the walls, along with the hand tools of her craft. The air smells faintly of leather and glue and paper—the comforting smell of books.
It was this smell that first attracted Vaughan to the craft of bookbinding. She was a student on sabbatical in London and looking for a part-time job. Noticing an advertisement in the window of a bindery, it took her three days to work up the courage to apply for the job. By the time she sailed back to the U.S. on the boat her husband had built, she had the tools and skill to bind their ship’s log, albeit with dental floss.
With light flooding in through the large picture window overlooking the Hudson, Vaughan explains how each job is done in multiple stages. Often she will leave work in one of the heavy metal presses while the homemade wheat paste dries. To keep business moving, Vaughan works on several projects at once.
On display is a historic ledger with well-thumbed covers that have come asunder. She’s been able to salvage some of the marbled end papers, and the pages of graceful copper plate are in good condition. Once she’s repaired the spine and attached new covers, the book will last another 150 years.
She’s also working on a new three-volume manuscript. Vaughan has cut the pages down to size and stitched them together with a saddlers needle. Carefully constructing the spine with headbands to prevent it from breaking when pulled from a shelf, she’s now ready to attach the boards for the cover. There are many ways of finishing a book: these volumes will have a combination of leather and marbled paper. Vaughan sources the leather from Pergamena, a local tannery in Montgomery. Lastly, she will use a finishing press to hold the books steady while she titles them using gold leaf.
Vaughan calls her work “glorified packaging,” but obviously takes great pleasure in it. “I’m always trying to figure stuff out. It’s really fun problem solving,” she says. In addition to her restorations and private press work, she designs and crafts display boxes and portfolios for artists.
After 40 years in the craft, Vaughan continues to hone her skills. “You find who’s good and study with them... make a pest of yourself.” She recently took a master class where she was humbled by how much she still needs to learn about applying gold leaf freehand. She’s also eager to pass on her skills and teaches once a week at SUNY New Paltz, fledging the next generation of bookbinding careers.