Junkyard arts and crafts
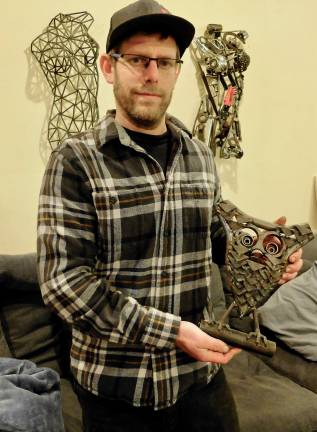
Tim Fields’ garage is crammed with buckets, filled to the brim with old machine parts. His scrap collection overflows into temporary storage in his driveway. Fields, who lives in Stillwater, NJ, has a career that many would envy: he builds and maintains race cars. He has an equally all-consuming passion, combining scrap metal and discarded steel parts into art pieces and sculptures.
Fields’ passion for building started with Legos. “My father tinkered with cars, machines and tools. So even at a very young age I was helping him and learning about how things work, and what to do when they stop working correctly,” he says. “I’ve always had tools in my hand.”
He learned early to be a fearless maker, experimenting with plastic model kits, recombining them into his own designs.
After high school, he studied horticulture before enrolling in automotive school. Fascinated with racing trucks built for the Baja 1000 off-road motor race, Fields moved from New York to Arizona following his dream of working on them. The recession hit and no one was spending money on high-end racers. Instead, he got a job in a car dealership working on street cars—great experience, but not what he had in mind.
Fields moved back to the Northeast. He grew up in the Finger Lakes and has always been a lover of the outdoor life. Building features for the downhill mountain bike course at Mountain Creek in New Jersey was a fun job and a good way to meet people. As luck would have it, a fabrication shop in Vernon that builds a dirt-modified racing car put out a call for welders. Fields was the perfect candidate. Finally, he was building race cars.
One lunchtime, he began playing around with discarded scrap metal. “I called it Lunchtime Arts and Crafts,” he says. “This stuff all gets thrown away, so why not use it?” The first thing he made was an owl.
“I realized I could go to scrap yards and get gears and all kinds of things,” Fields says. Soon he was experimenting after work, too. He made a robot from transmission parts, a dragonfly from a dismantled motor, a spider from gears, a working motorcycle from a chopped up bicycle. He shared his pieces online and folks clamored to buy them.
His metal art caught the attention of one of the leading car customizing companies on the east coast and Fields jumped at the chance to work on cars he’d only ever seen in pictures. A year in, despite the excellent pay and experience, the five-hour round-trip commute to Yonkers proved too much. It was time to move on, this time to a race car fabricator in Pennsylvania working on vintage Porsches. In addition to building, he got to be part of the pit crew, travelling to races around the country.
After work and on weekends, Fields was going deeper into his metal art. Working with a MIG and TIG welder, he began challenging himself with more difficult projects. “I was trying to build stuff and I couldn’t find the parts that I needed,” he says. There was also a dawning realization that he was done working for other people. He was ready to focus on setting up a micro shop in his garage and building his own metal art business, T.F. Metalfab.
Fields invested in a computer driven plasma cutter that cuts shapes from metal. It came in pieces and he had to learn how to assemble, program and design for it, a trial by fire that paid off. “I can use this machine to make my Lego blocks,” he explains. “I can make literally any part I need.”
Commissions paid the bills, but Fields’ main inspiration comes from the scraps themselves. It might be a giant bolt, an auger from a food prep machine or the rusted tank of an old motorcycle. “One tiny little piece will make me think of an entire thing.” As soon as he posts a new work online, he finds a customer, often while the piece is still hot.
Casting back to his past, Fields came across an art project from elementary school—a human mask made out of multiple thin strips of clay. “That inspired me to do something in metal. What if I got a mold and made something with steel? I searched on eBay for a long time until I found a mannequin that I liked.” Once he’d made a cement mold of the mannequin’s torso he had a form to work within. He created a series of large female sculptures by welding together metal scraps, small steel strips, nuts and bolts, and even tools.
For about a year Fields devoted himself entirely to metal art, commissions rolling in so fast he worried he couldn’t keep up. He’d proved to himself that the potential was there to make a living from his art, but to do that he’d need to grow the business, take on an assistant and find a larger space. Fields loves the community of talented craftspeople that surround him in North Jersey, but realizes that his dream of building that shop will most likely happen down south, somewhere the cost of living is cheaper.
For now, he is the lead fabricator and mechanic for the Heinlein Racing Development company. During race season as part of the pit crew, he spends several days on the road every other week maintaining endurance race cars. In his spare time, he makes art.
“My ultimate goal is to build a container home and be as self-sufficient as we can be,” he says, of himself and his partner, Audrey. “I can build my house out of scraps!” Down the road, Fields envisages being a fly-in technician for a pit crew, working the race, then flying home again to his own metal art shop.